Beschreibung
Wichtige Erkenntnisse
- Rethink how you’re using BIM in the supply chain planning process.
- Learn how to implement tools and processes using BIMBAU to collaborate.
- Learn about improving project performance by allowing procurement planning and direct connection from vendors in the design phase.
- Learn about applying new technologies that will allow construction projects to be on time and within budget.
Referenten
- Andres RojasCTO at one of the most amazing startups in LATAM, that is gonna change the way the world builds! Senior Software Engineer with over 15 years of experience building tech-based products for multiple markets like Asia, Europe, and the Americas. Specializes in Product Development for Startups, Growth Hacking, and Tech Team Building for compelling Startups. Worked with First Rock Capital for five years as Head of Engineering, helping Startups overcome technical challenges and Product/Market fit challenges. Also, participated as a Mentor for Product Development for Apps.Co (A Colombian Startup program led by the Ministry of Technology) helping over 50 Startups along the process. Serial entrepreneur with vast knowledge of creating, growing and scaling products in multiple markets.
JUAN SALDARRIAGA: Hi, everyone. It's our pleasure to present BIMBAU-- Reshaping Productivity Through BIM, Supply Chain, and Collaboration. Let me introduce myself. My name is Juan Saldarriaga. I am the CEO and co-founder of BIMBAU. My background is civil engineer and supply chain manager.
I have been working in this sector for more than 16 years, and I manage one of the biggest areas of supply chain in Colombia.
ANDRES ROJAS: Hello, everyone. My name is Andres Rojas. I'm the CTO and Co-founder at BIMBAU. I'm a Senior Software Engineer and Product Manager with over 14 years of experience creating tech products and startups. I'm also a tech evangelist and a speaker.
JUAN SALDARRIAGA: Before to begin with our presentation, we want to explain a little bit more about BIMBAU. BIMBAU is a multi-service platform in which we collect all the information from suppliers in a marketplace. Then, with all the information, we convert this material in 3D elements of BIM objects that will be used by designer for the models. With quantities and prices, we help contractor and subcontractor to get the best prices and planning of all the supply chain. At the end, we have all the profitability of the supply chain cycle in which we can close the gap of productivity related with the supply chain.
ANDRES ROJAS: In this talk, we're going to talk about our experience building the first BIM-powered procurement ecosystem in Colombia. In this time, we have discovered some of the biggest issues in the industry, possibly globally. One of the first things that we discovered is that the ecosystem is so disaggregated, it's so disarticulated, that it's causing huge gaps in communication between the key stakeholders.
Also, that supply chain is one of the biggest unproductive sectors in the construction industry. Planning is almost never happening. And when it happens, it fails because it doesn't attach to reality as much as it should. BIM is the best way to plan, but people are not using it because of the lack of quality of information available. It this talk, we're going to talk about what we discovered.
And the first thing that we discovered is that BIM in construction is broken, but it's not a fault of the methodology itself. So if we see BIM implementation and adoption, we see that every day, every year, BIM adoption is on the rise. We have been seeing the latest reports of this year, which states that BIM in construction globally, it's increasing. Just only in the USA, 98% of the largest firms of architecture are adopting BIM.
It's incredible because right now, we can see from 75% to 240% improvement in productivity by correctly implementing BIM. We also can see that if a project is implementing BIM in the right way, 25% increase in productivity of labor can be happening. This is amazing, but it is also a contrast because the culture that we're dealing with every day poses multiple obstacles.
We have seen managers, company owners, architects that are still stubborn to change. They have a huge fear of change. Their ego doesn't allow them to accept the benefits of implementing BIM, and this allows companies to live in the past and just not to move forward. So we're going to share with you some of the key things that we have learned in the process.
The first one is about the people. People do not understand BIM. And this is something that is really hard for us to understand because for most of them, BIM has become a buzzword. People just use it to impress other companies or to just add some information to their websites because they say they implemented BIM, but they don't fully understand what BIM is.
Quantities and prices are a part of the BIM mythology, but it hasn't been detailed as much as it should be yet. Also, we have seen that when people find projects that are BIM-based, they stop bidding for them. They tend not to apply for those kind of contracts because simply, they do not want to get involved into the whole complication of working in a BIM-based project.
We have even seen that people ask us how could they install BIM in their company as if it was some kind of software or some plug and play hardware. So they don't truly understand that BIM is a methodology and not just a software you can install in your company. Now, we have seen also that C-levels or even developers or clients, they really love BIM. But when you start going down the value chain of the construction lifecycle, you start seeing that contractors and subcontractors, they hate BIM because they have problems understanding the 3D models or even they have problems with the software that is required to be able to understand the designs.
Something that we have discovered about the methodology versus the reality is that in construction projects, things happen every day, and it's almost impossible to keep the model updated due to the changes and the specification change orders, even issues with the construction site. There's also problems when we try to match the materials that are invoiced to those installed or used in the construction project. It is almost impossible to know for sure that you have installed exactly the same materials that you say that you purchased.
Also, it is impossible to guarantee for 100% that there were no cutting corners in the process of the implementation of a project. When we see BIM in the market, we see that vendors and suppliers are the ones that have to pay for the BIM libraries. They have to pay for the hosting, for the modeling, and for everything required to publish their BIM objects to the web.
But they tend to receive the less value from it, which causes a problem because as they do not have enough motivation to do it in the right way or to find the people that can do it in the right way, the quality of information of the BIM objects are very poor. That causes a very huge gap because when architects and designers are trying to use these models into their designs, we end up with designs that lack quality of information.
Also, when you see the entire market and the available BIM objects, you see that supply chain is not even taken into account in the process. For us, it doesn't make sense. BIM has the potential to change the way the world builds. It has the potential to change the entire industry around the globe. We are now responsible for 38% of the global CO2 emission. We are the second worst in productive industry in the world.
We lose almost $3 trillion per year due to inefficiencies. We have the power to become the number one promoter of progress. We should be the ones that are leading the race against global warming. So we just need to find the right path.
JUAN SALDARRIAGA: OK. The good news is we can change and bring productivity back to construction. The best way to do it based on our background is to bring supply chain planning and collaboration to BIM and the best way to recover $320 billion that we lost every year because we have [INAUDIBLE].
The best way to do it is to transform the way that we do. Normally, people would separate. We have designers, supplier builders, working separate, disaggregate. But what we want to do is bring all of them together in an early stage to make all the plans of the supply chain. Also, we want to invite you to bring a new dimension in the BIM dimension model because if you go to see even the 10 dimension that sometimes people talk, there is not anything related with the planning of their resources, supply, or materials.
We want to bring you-- 4, 5, 4, 3, 2, 1. Reports continue we want to let you know, we want to share-- 5, 4, 3, 2, 1-- on the supply chain management, it's really important for everyone. The supply chain is the way to plan, execute, and control all the material and services that will arrive to our projects with less real cost, and also to better planning and coordination in the execution of the processes more capability for suppliers and also to builders and subcontractors-- better logistics.
That means less CO2 emissions in every project, prevent material defects, and obviously at the end, clients satisfied and happy. And what happens when we combine BIM methodology, data, and supply chain management to the process? Finally, we have the best formula to bring productivity to construction.
Imagine this combination is the best formula to get productivity in our projects. Imagine that BIM with supply chain is a really good formula. But we have data starting by supplier with a lot and good information for their own products, we can bring the best solution to increase productivity. Imagine Not only information about products, what happening we have real-time inventory from our supplier-- new material, new and very good vendors, and a lot of recommendation of materials that are closest to my project.
In terms of time, imagine [INAUDIBLE] real-time location of our products ready to come to our project. It's the best way to get the just-in-time material within our projects. Another less waste of material at the end of every process. Imagine the cost. What happens if we have the real-time prices in our BIM model? The total BIM model in real-time with prices and cost prediction?
After the coverage, everybody understand the [INAUDIBLE] prices. And we have great information of what is going to happen in the following month. What happened if we had the prediction? Imagine this kind of information.
In terms of sustainability, imagine new materials. We can have substitutes from materials that are really good for the atmosphere, for our eco-friendly system, and we can get less CO2 emission measured. And finally, imagine an operation when anybody needs to do anything, we can get there to measure our processes and repurchase of all the materials. At the end, the idea is to get the best information related with BIM and also bring the best planning of supply chain to the process.
We need a new dimension [INAUDIBLE]. Is that the invitation that we want to bring to you-- invite you to be part of the global community improving productivity in the construction sector. We truly believe it's the best way to recover $320 billion per year. Thank you very much.
Downloads
Tags
Produkt | |
Branchen | |
Themen |
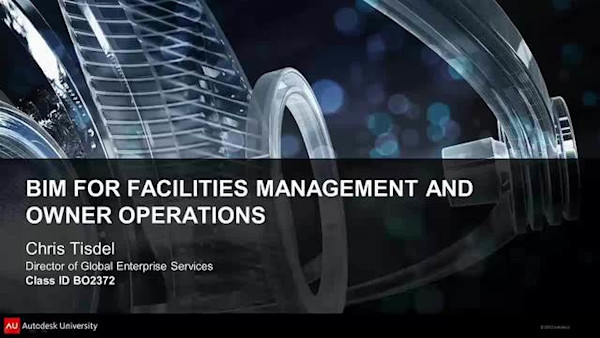