Descripción
Aprendizajes clave
- Learn how to implement AEC simulation best practices in Autodesk CFD.
- Learn how to apply relevant modeling strategies for airflow and heat transfer.
- Learn how to assess Autodesk CFD results for better designs.
- Learn about identifying opportunities for design optimization.
DR MUNIRAJULU M: Greetings and welcome, everyone. Thank you for joining this session about better HVAC designs using Autodesk CFD simulation. We will go through how Autodesk safety simulation is implemented in the design of air conditioning system for an international airport expansion project.
Let me introduce myself. My name is Dr. Manirajulu. Currently, I am responsible for CFD Analysis in MAP AEC design for buildings and factories in L&T construction, Larsen & Toubro Limited India-- L&T in short. L&T construction is India's largest construction organization and ranked among the world's top contractors.
The company's capabilities span the entire gamut of construction-- civil, mechanical, electrical, and instrumentation engineering, designing and building landmark and iconic projects. I use simulation technologies and tools extensively in the design of buildings. I have more than two decades of experience in using CFD technology for design analysis, validation, and optimization.
I use CFD simulation in the design of airports, data centers, high speed rail stations, depots, convention centers, stadiums, large office buildings, residential buildings, and factories. I have been a regular speaker at Autodesk University since 2017, both in the US and India events. And it has been an enriching experience being part of the AU learning community.
I'm sure you will find the session interesting and useful. Before we jump into the session, let me give you an overview of the international airport expansion project. This is the external view of the airport. The original building is T-shaped. You could see that T-shape here.
And the expansion gives it the shape of a bird with wings spread. So here you can see that. This is the expansion portion. The airport complex consists of many different buildings and facilities, such as runways, aprons, passenger terminal buildings, cargo terminal, air traffic control towers, and aircraft hangars.
The International Airport is designed as an international and domestic hub with ultimate capacity to carry 34 million passengers per annum from 12 million passengers per annum. That's almost three times increase. Our focus in this case study is Passenger Terminal Building, PTB in short, as seen in this image.
The Passenger Terminal Building has a total area of 120,000 square meters and consists of functional areas over 7 levels, namely level B through H. And being expanded to a total area of 370,000 square meters. So you can see the levels in the cross-sectional image here.
Within the Passenger Terminal Building, level D is baggage reclaim area in the arrivals section and is being expanded by 21,000 square meters from existing 9,000 square meter. The existing baggage reclaim area is this portion. And it is being expanded on both sides-- the light-colored portion here.
The existing one is 9,000 square meters. And the total expansion is about 21,000 square meters. Similarly within the Passenger Terminal Building, level F is the check-in hall area in the departure sections, and is being expanded by 21,000 square meters from existing 9,000 square meters. Similarly, this is the existing portion. And on both sides-- that is east and west, both sides-- it is being expanded by 21,000 square meters.
Both the check-in hall and baggage reclaim are passenger circulation areas with large spaces. And environmental conditions are critical for passenger comfort. Air conditioning design and its verification by CFD simulation is important to ensure a comfortable environment for passengers.
HVAC design conditions are based on specified outdoor conditions for summer and indoor conditions for passenger comfort. For CFD simulation, this design parameters along with external and internal heat gains are used as input data for the CFD models. Air conditioning system is a chilled water-based system with centralized chilled water supply.
The conditioned air distribution takes place through floor mounted air handling units, binnacles, and air terminal devices. Jet nozzles and slot diffusers are used as air terminal devices in the check0in hall, whereas drum louvers or drum jet diffusers-- they are used as air terminal devices for the baggage reclaim area. With this introduction, let me move on to key objectives.
We will cover four key learning objectives as we proceed, namely best practices in Autodesk CFD, modeling strategies that we have used, and CFD results that we have obtained, and how we have used the CFD results as opportunities for design optimization, as well as to come up with better HVAC designs. Hopefully at the end of the session, you will be able to appreciate how simulation CFD helps in the design process.
The goal of CFD simulation is to evaluate if the design meets the performance requirements and to explore opportunities for design optimization based on simulation results. We will go through these topics one-by-one in this session. Let us explore some of the best practices in AEC simulation.
First and foremost, key feature for a successful CFD simulation is how we characterize our idealized building components and other geometrical features for CFD modeling. Large spaces and many components with tiny details, as common in AEC applications, need to be simplified through characterization. Features characterized in CFD modeling for airport air conditioning analysis are people, or occupancy, air terminal devices such as slot diffusers and drum louvers.
Characterization is a strategy to capture design intent with the minimum amount of necessary complexity to optimize simulation performance in terms of ability to mesh, reduce Solver time, and produce valid results. While fully developed building model is necessary for construction, most of the geometric complexity may not be required when leveraging simulation for obtaining reliable performance insight quickly and effectively. It is important to keep the big picture of simulation goal in mind during the characterization process.
And how this process can reduce simulation complexity. The important considerations are physics of the problem, the manufacturing specs of the component. How do we use less detail without losing impact of the component on flow pattern and heat transfer?
Here is an example of diffuser characterization. This diffuser has many small air gaps and thin metal veins that would require a small element size to capture flow accurately. The diffuser has small details with respect to the room it is supplying. And explicitly modeling these details would add to CFD meshing and solving complexity.
Hence such a component can be characterized as shown in this image. A single diffuser is modeled explicitly, and velocity components are obtained-- VX and VY components. These velocity components become inputs to the simplified model, where inputs are velocity components and the geometry details.
These details are not modeled explicitly. So this is what we call as a characterized model. Another example of characterization is people, or occupancy details. Airport departure and arrival halls are circulation areas where people keep moving about for checking and baggage reclaim. Modeling occupants with all possible details computationally may not be practical. Hence human occupancy is modeled as air volume of human height and heat generated by humans assigned to it.
A best practice that could be very important in terms of appropriate physics is use of mixed convection. Air conditioning in Passenger Terminal Building is by mechanical ventilation, wherein air movement is driven by fans to provide air changes within the occupied space. That is replacing stale air with fresh air as well as removal of heat by force convection using fixed air properties. This results in human comfort and good indoor air quality.
However, in CFD modeling, it may be necessary to include the effects of buoyancy using variable air properties apart from force convection to properly capture airflow and heat transfer. In this project, mix convection approach is used to account for buoyancy in check-in hall and baggage reclaim hall.
In the following section, we will go through modeling strategies we followed for airflow and heat transfer in this project. Modeling strategies, or workflows we followed are basically creating a CAD model and preparing a CFD model based on that with component characterization wherever is required, then assigning materials, specifying boundary conditions, meshing and Solver settings. These are the workflows typically we follow in a CFD modeling and analysis.
From Revit, a CAD model suitable for CFD simulation is prepared. And input details for a CFD model include the building geometry from CAD data with the major architectural layout as well as interior details such as check-in counter, service counters, rooms, walls, floors, roof, and inlet and outlet extensions. So all the details that are required for flow and heat transfer are included.
And wherever the geometry needs to be simplified, it is simplified. This is a snapshot of simplified CAD model for baggage reclaim hall. We have included the 11 details for flow-only transfers, such as baggage conveyors, binnacles, columns, and other building details.
Two types of supply diffusers are used in check-in hall, namely nozzle jet diffusers and slot diffusers. And the sizes used, we have indicated by arrows for your information. The nozzle jet diffusers are modeled as per actual geometry for the supply of air conditioned air, whereas slot diffusers are modeled as characterized geometries. When the flow is in the normal direction, the CFM with free area ratio is used in the slot diffuser modeling.
When the flow is angled, velocity components are applied on the characterized slot diffuser geometry to capture the flow. Drum louvers are modeled as characterized geometry with free area if flow is normal to the drum louver supply surface. When the flow is angled, velocity components are applied to the characterized geometry to capture the flow. Very important in terms of flow pattern, and fluid flow simulation in the CFD modeling.
So here you can see supply in inlet CFM and supply temperature are specified as boundary conditions on the nozzle jet diffusers. Similarly, supply CFM and supply temperature are applied as boundary conditions on the drum louvers. Next very important step in the CFD analysis-- materials. Assigning materials.
Materials define the properties of parts which impact the physics of simulation. Simulation CFD provides a comprehensive library of materials along with the ability to define custom materials as needed. For AEC applications, air is by far the most common fluid material.
For check-in hall and baggage reclaim hall in this project, for the CFD simulation, we have used fluid domain as air material with fixed properties. That means density does not vary with temperature. So here you can see that assigning fixed properties to the air material.
Based on local hotspots observed during CFD simulation, air properties are changed to variable. That means the density will vary with temperature. This is done to capture any buoyancy effects that may be present.
Outlet grills are assigned default resistance material to give resistance to the flow with a free area ratio of 0.5 or 50% open area to the flow. Air is mechanically moved in and out of the building space, so inlets are assigned volume flow rate on each supply inlet or diffuser. And this arrow direction indicates that the flow is in the right direction from the supply or the inlet diffuser.
That is, the flow is in that direction, towards the occupied space. So here we have assigned flow rate and temperature as a boundary condition. Slot diffusers with angled flow are applied with velocity components after characterization and testing with a detailed geometry. This is the detailed geometry.
And then we test it with a single slot diffuser. And then based on that, we characterize the diffusers to be used in the CFD modeling. Here we see similarity in flow pattern between the detailed slot diffuser model and the characterized version of it. The flow pattern is very similar, except close to the inlet areas.
Here we can see the resulting flow pattern in the check-in hall using the technique of characterization. Using technique of characterization, we would obtain the velocity components in x direction and y direction. And these are specified as component velocities on the surface of the slot diffuser geometry without explicitly modeling it. And then we get the effect of the flow from the diffuser.
And another important boundary condition-- outlets. All outlets here are applied with volume flow rate boundary condition, except one outlet, where pressure boundary condition needs to be applied. This is required to get a numerical solution to the flow. Here you can see the pressure boundary condition-- 0 gauge pressure is applied.
Thermal simulation is driven by thermal boundary conditions and deals with internal heat gains from people, equipment, and lighting. External heat gains include solar and transmission loads. These are taken care by defining total heat generation boundary condition-- total heat generation boundary condition for the occupied volume.
People load, equipment load, solar load are applied over a volume of 1.8 meter height from the floor. Transmission load is applied on the facade surface in terms of mu values and design outdoor temperature. And in the check-in hall or the baggage reclaim, the lighting load is important. And the lighting load is applied on the bottom surface of the ceiling.
So with that, we have included all the input data to the CFD model in terms of boundary conditions, design data. And now we will proceed to meshing. Automatic mesh sizing is used to define the mesh distribution in the CFD model domain. CFD simulation uses FEM-- Finite Element Method-- to calculate the fluid flow and thermal results.
The finite element, FE mesh, is the backbone of CFD simulation and has a direct impact on solution accuracy. In Meshing Task, the model geometry is divided into many smaller regions called elements, where each corner of the element is a node at which flow and thermal variables will be calculated. For simulation, a certain number of elements will be required to adequately capture flow and thermal characteristics.
As element count increases, so does the solution time and hardware requirements. The question is, how many elements would be required? Well, we use just enough for mesh-independent solution for better accuracy.
Plus we do automatic mesh sizing for the entire domain. And then we do refinement on volumes as necessary. Local mesh refinement with uniform mesh is used for mesh on supply diffusers the way it is shown here to capture the flow through them. Next-- Solver settings.
The Solve dialog in the simulation task is the command center for simulation. It controls the physics of simulation as well as what data are to be output. Solver settings are based not only on the physics of the application, but also user preferences such as how much data is to be output. The Solve dialog is comprised of three types-- control, physics, and adaptation, each of which have a variety of input fields and buttons. Simulation CFD has the capability of solving a wide variety of fluid flow and heat transfer applications.
The first step to knowing which settings are required is to determine the physics of the problem being solved. In this case, flow is solved first with steady state and with intelligent solution control enabled with fixed rate properties. Heat transfer is to be considered in this analysis. So heat transfer is enabled, as you can see here in the solution settings with flow as incompressible.
Advection 5 is used, as it is the recommended scheme for most flow analysis. After solving a certain number of iterations, temperature field is checked. And if local hotspots are present, then air properties are changed to variable with intelligent solution control switched off.
Buoyancy effects due to gravity need to be considered to account for the mixed convection effects. So gravity is enabled here. You can see gravity is enabled here. And heat transfer happens by mixed convection now. And this would capture the buoyancy effects present in the solution domain.
After simulation is set up, run, and converged, we can look at results using results visualization tools in Autodesk CFD simulation. We can visualize performance characteristics such as temperature, velocity that are difficult to capture in the real world at all locations. Airflow velocity and the temperature values are the key results from CFD analysis to evaluate thermal comfort.
Results plane in this image provides flow pattern from drum louvers. This is a drum louver location. And you can see the flow pattern from the drum louvers in the baggage reclaim or for the baseline design.
This gives a visual picture of how airflow happens from the drum louvers into the occupied space. Results plane in this slide provides velocity distribution in the occupied space for baggage reclaim hall for baseline design at 1.8 meter from the finished floor level. This helps us to look at local variation in velocity values and the local values from point to point. We will get that information here.
Results plane in the slide provides temperature distribution in the occupied space for baggage reclaim hall for the baseline design at 1.8 meter from the finished floor level. This helps us to evaluate local variation of thermal comfort condition in terms of temperature. So this is the temperature distribution within the baggage reclaim hall.
Here we notice a few hot spots. Hot spots are areas where temperature is more than the required temperature, and of course, which is not acceptable. Results plane in this slide provides velocity distribution in the occupied space for optimized design for baggage reclaim hall at 1.8 meter in the finished floor level.
Results plane in this slide provides temperature distribution in the occupied space for optimized design for baggage reclaim hall at 1.8 meters from the finished floor level. Now if you notice here, the hot spots are eliminated. In the previous slide for the baseline design, we saw there were three hotspot areas. And now with the optimized design, these hotspots are eliminated and the occupied space meets the indoor design temperature requirement, which is 24 plus/minus 1 degree Celsius.
Now we come to the results for the check-in hall. This results plane in this slide provides velocity distribution in the occupied space for check-in hall for the baseline design at 1.8 meters from the finished floor level. And here you can see non-uniform velocity distribution with low velocity areas less than 0.25 meters per second are observed.
This is a direct correlation to the temperature that will result from this flow, which we will see in the next slide. So the results plane in the slide provides temperature distribution in the occupied space for check-in hall for baseline design at 1.8 meter from the finished floor level. Here you can see non-uniform temperature distribution with many hotspots.
And these hotspots occur at low velocity areas, as we have seen in the previous slide. We have low velocity areas. And these hotspots occur at those low velocity areas.
Our results plane in this slide provides-- this is velocity distribution in the occupied space for optimized design for check-in hall at 1.8 meter from finished floor level. Here you can see uniform velocity distribution with most of the occupied area with velocity greater than 0.25 meters per second. Results plane in this slide provides temperature distribution in the occupied space for check-in hall at 1.8 meters from the finished floor level.
So here you can see uniform temperature distribution without hotspots. And this occupied space or area is now within 24 plus/minus 1 degree Celsius for the optimized design. So far, we have seen the optimized design provides required indoor temperature. In the next section, we will go through how we arrived at the optimized design for the check-in hall, though a similar procedure is followed for the baggage reclaim hall also.
Here you can see the baseline design for the check-in hall. And this temperature plot indicates as we have seen earlier. So there are hotspots present in the occupied area. And the temperature of these hotspots are above 31 degrees Celsius, which is clearly not acceptable.
So based on the baseline results, which are not acceptable, design changes made with respect to diffuser angle and the CFM values-- that's the flow rate values. And these changes are intended to direct the flow towards the hotspots. So let us call that design option 1.
So here you can see the jet nozzles are straight. And here we have jet nozzles at an angle. When we compare the temperature results of design option 1-- this is temperature results of design option 1-- with baseline design, we notice that the extent of hotspots, the extent of these red areas, have now been reduced in the design option 1.
Based on the improved results of design option 1, a design change also is made in the architectural layout. That is, there is a glass panel present here. And this glass panel has been now removed in the design change. Let's call that design option 2, where we have removed the glass panels.
So this is the architectural layout change with respect to option 1 in the 3D view. So these are the glass panels in the design option 1. And in design option 2, that has been removed.
And when we compare the temperature results of design option 2 with the design option 1, what we notice is the extent of hotspots is reduced significantly. And moreover, the hotspot temperature, which was in the range of 30 to 35 degrees Celsius, now is reduced to 28 30 degrees Celsius. Considerable improvement.
In design option 3, additional CFM is introduced towards the hotspot area. And diffuser angles are changed from previous 15 degrees to 20 degrees. And when we compare the temperature results of design option 3 and design option 2, we notice that the extent of hotspot areas is not changed much.
So there is not much of a difference between option 3 and option 2, which means that we have to look for another design option. And in design option 4, the CFMs were revised. CFMs were modified on select diffusers and almost doubled, increased from 552 CFM to 1,200 CFM.
And these three diffusers are pointing towards those hot spots. Now when we compare the temperature results of design option 4 with the design option 3, what we see is that the extent of hotspots is reduced and most of the occupied space is within 24 degrees Celsius-- this blue area. Most of the occupied spaces colored as blue, indicating the temperature there is within 24 degree Celsius.
And when we use mixed convection by changing the air properties to variable, we notice that the hotspots which were existing in the design option 4 with force convection option, which was, the hotspot temperature was about 28 to 30 degrees Celsius, now the hotspots are completely eliminated in the design option 4 with variable air properties, which means the mixed convection is playing a role. And that has been captured well in design option 4.
So we have this check-in hall occupied space within 24 degrees Celsius, which is the design requirement. So in conclusion, we have seen that using Autodesk CFD, we are able to evaluate HVAC design and optimize the design so as to get better designs meeting the performance requirements for the airport expansion project that we have presented here. And using Autodesk CFD for the air conditioning analysis, we get very important results, insights to check the design adequacy.
And one of them is the airflow velocity values and patterns. This actually gives us a measure of air quality and how the cooling is happening. The second one is the temperature values and distribution. And this gives a measure of thermal comfort.
So to wrap up, the air conditioning design analysis using Autodesk CFD provided us a basis to conclude that the design is adequate for thermal comfort in Passenger Terminal Building of an international airport. Thank you for listening. And have a nice AU 2022.
Downloads
Etiquetas
Producto | |
Sectores |
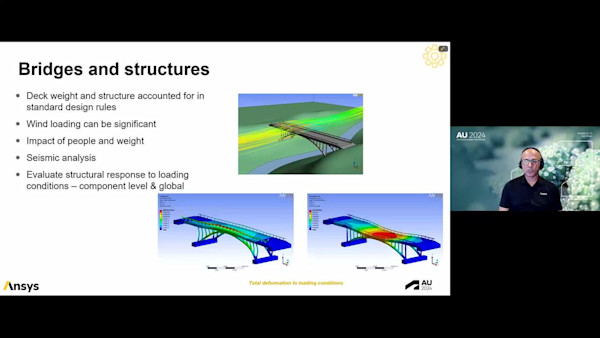
Advancements for Simulations in Built Environment
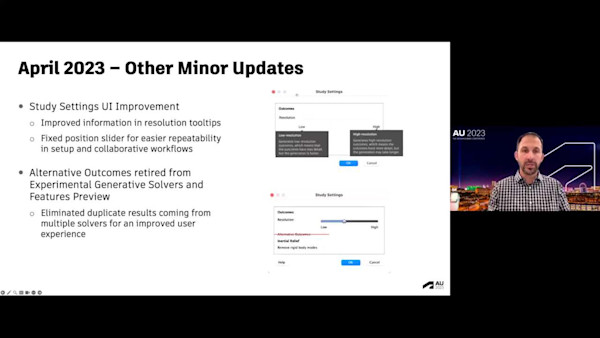
Success with Generative Design in 2023
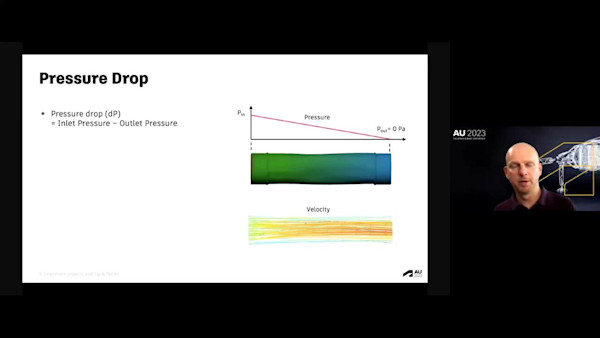